■経営難のポルシェを救ったのはトヨタだった
ここで一つのエピソードを紹介する。
戦前からクルマを作り続けてきたドイツは、戦後も古い生産システムから抜け出せずに苦労していた。その理由を分析したことがあるが、最古の自動車メーカーとして知られるメルセデス・ベンツや技術集団のポルシェは徹底して良質なモノづくりにこだわる「マイスター制度」で支えられていたが、このドイツのマイスター制度こそが硬直した生産システムの原因であったと私は睨んでいる。
マイスター制度は中世の時代から受け継がれた歴史を持ち、手工業者が集まって一つの共同組合を形成し、その組合に入ることで修練技術を守る制度である。ちょうど江戸時代の職人徒弟制度に似ている。とにかく親方に見習いとして修行することで高い技術、見識、経営手法などを学ぶわけだ。
しかし、1980年代に起きたドイツのピンチは戦前から続いたドイツの強みであったマイスター制度が足かせとなり、グローバル化によるクルマの多様化に対応できなかったのだ。ドイツの強みが弱みになったと私は考えている。
1990年代にいよいよ苦境に追い込まれたポルシェを救うために、フェルディナント・ポルシェ博士(創業者)の孫にあたるフェルディナント・ピエヒ氏(当時のVWのグループのCEO)は、ある計画を練っていた。それは米国系のベアリングメーカーにいたヴェンデリン・ヴィーデキングをポルシェのCEOに抜擢し、積極的にトヨタ式生産システムを取り入れた。職人気質でプライドが高いポルシェのエリート技師はそれまで自分たちが設計したクルマが、「生産現場では作りにくく、生産性を悪化させている」という事実を理解していなかった。
コンサルタントとして雇われたのはトヨタの生産システムを熟知する元トヨタマンだった。彼は始めてポルシェの生産現場をみて驚いたという。
「ポルシェの工場ではサルを飼っているのですか?」
と、その生産性の悪さを鋭く指摘したのだ。製産ラインで部品に不良が見つかると、工場の二階までハシゴに登って取りに行かなければならなかったので、あちこちでハシゴを登り降りする姿が「サルの木登り」のように見えたのだ。
ポルシェはリーンマネージメントというトヨタ譲りの生産システムを採用し、全社員には「ポルシェ・インプルーブメント・プロセス」(PVP)を展開した。
もともと持っていたポルシェの潜在的な能力を高め、生産効率を徹底的に見直したのである。こうしてどん底から這い上がりながらポルシェは急成長したが、トヨタのおかげと言っても過言ではないだろう。
参考までに述べると、トヨタ式生産方式をもっとも理解していたのはフェルディナント・ピエヒ氏である。1988年ごろにドイツのシュピーゲル誌のインタビューで、「私は日本に非常に感銘している。日本人の勤勉,規律,彼ら民族の信じがたい力,結束力。私はこの国を賞賛するし、夢が叶うなら、トヨタかホンダで働きたい」と記している。(参考文献:『フォルクスワーゲン社とポルシェ社 ― 同族統治と企業統治の狭間で。』 第3章「日本の誘惑」Verlockung Japans 吉森賢著)
■トヨタの「強み」が「弱み」になる
ポルシェやメルセデスでも、それまでの強みが弱みになることは130年の自動車史で明らかであるように、いままで自前主義で成長してきたトヨタの強みが弱みに転じるかもしれないと筆者は感じている。
トヨタはあらゆる領域の技術を自ら研究することで、モノの本質を突き止めることに技術者としての生きがいを感じているが、こうした傾向はトヨタだけではなく、ホンダも強い自前主義を貫いている。
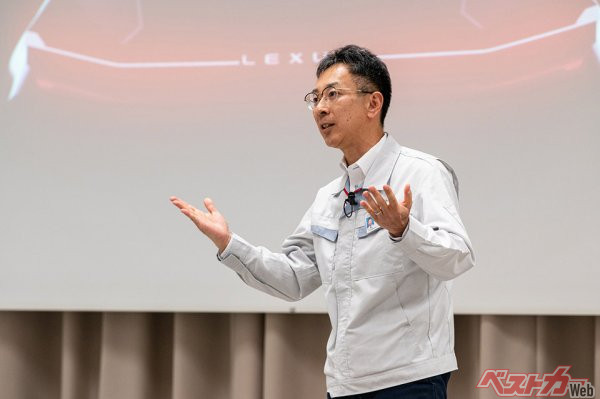
しかし、いま直面している電動化や自動運転を技術革新するには、この自前主義が仇となるかもしれない。自前主義は開発のスピードを低下させ、ライバルが標準化したとき、大きな遅れが生じる。というのは自前で研究してきたものとの乖離が生じ、それを埋めるのに時間とコストがかかるという悪循環が生まれるのだ。
設計の現場にいるエンジニアはその苦しみを知っているが、それも仕事だと割り切っている。
生産は効率主義だが、設計は非効率。
なにもこの問題はトヨタだけでは解決できない。早い段階から標準化を進めるには協調領域としての産学連携が不可欠だ。この産学連携が上手なドイツでは、先端技術は当たり前のように産学連携で研究し、その先にはISOなどの国際的な標準化を推し進めるコンソーシアムが引き受ける。
こうした協調領域のプラットフォームを基盤として、各メーカーの独自の競争が生まれるのだ。日本は長い間、この産学連携が欧米中と比べてもっとも遅れていたが、これは我が国の産業の大きな課題でもある。
技術的には遅れ気味なバッテリーやソフトウェアの技術を早期にキャッチアップする必要があるし、むしろ電動化時代では運動性能と高度運転支援(ADAS)の性能をさらに高める必要があるだろう。この2つの領域は顧客体験に直結する重要な競争価値ではないだろうか。
こうした課題を前にするとトヨタはいま重大な岐路に立っていると思われる。
【画像ギャラリー】トヨタのBEV戦略を占う画像と資料(4枚)画像ギャラリー
コメント
コメントの使い方BEVは元々やる予定だった全方位の一つではあるけれど、真の情勢見えていない株主用でもある
今後の世界がBEV一色になる未来は、有り得無いって事くらいトヨタも分かってます。でも一部モビリティにはEVも向くしバッテリーや関連技術高めるのにも繋がる
そしてトヨタ自身が言った言葉たち。誠心誠意説明しても聞いては貰えないし、自国も変えてはくれないし、他国は間違い認めない。それ心得ての実行を始めたトヨタは強い