最近、新車の試乗記のなかに、新しいプラットフォームを採用したことによって、ボディ剛性が高くなったとか、軽量化してよくなった、などとよく書かれるようになった。
そもそもボディ剛性とは何なのか? 最近、スバルのSGP、トヨタのTNGA、ダイハツのDNGA、日産のCMF、スズキのハーテクトといった、各社新型のプラットフォームをニューモデルに投入してきているが、そうしたプラットフォームと関係があるのか?
そこで改めて、ボディ剛性が高いと、どのような恩恵が得られるのか? 逆にネガな部分はないのか?
またプラットフォームが新しくなったことによってクルマはどう変わるのか、自動車テクノロジーライター・高根英幸氏が、なるべくわかりやすくかみ砕いて解説する。
文/高根英幸
写真/ベストカー編集部 ベストカーWEB編集部
ボディ剛性が高いクルマと低いクルマの違い
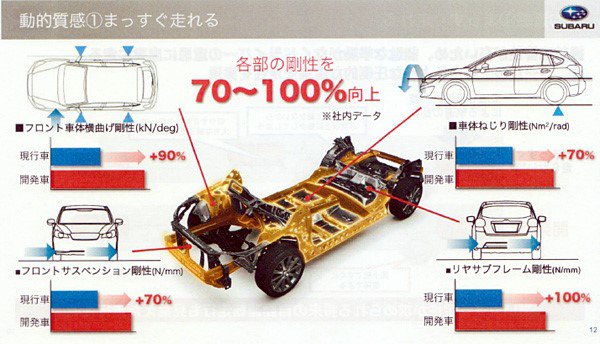
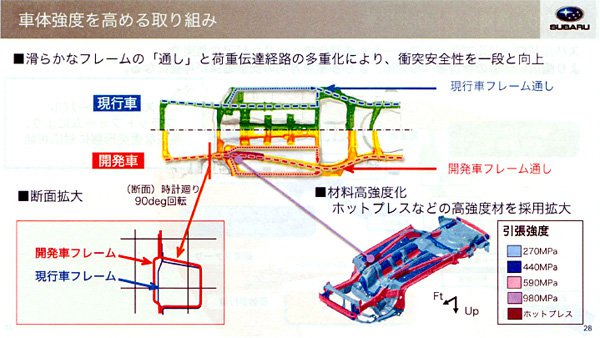
クルマの走りや乗り心地には、すべてボディの剛性が大きく関わっている。剛性とは変形のしにくさを示す強さで、剛性が高いほど力を受けても変形しにくいことになる。
走行中、クルマは路面からの衝撃を受け止め続ける。タイヤやサスペンションが吸収し切れない振動はボディに伝えられるが、この時にボディ剛性が低いとボディはブルブル、ワナワナと震え乗員に不快な印象を与えてしまう。
ボディ剛性が高いと車内に振動は伝わりにくく、衝撃を受け止めて外へと逃がす。ボディ剛性が高い方が、同じ固さのサスペンションでも足は良く動き、結果として乗り心地は向上する。
我々、モータージャーナリストが試乗記で「ボディ剛性が低い」と表現するのは、大抵は路面からの入力がどれだけボディを揺すっているのか体感して評価しているもので、ボディ剛性が高いことが良いクルマの基本となっている。
ドアの開閉でボディ剛性を感じる、という記述も見かけるが、これはドアの密閉性やドア自体の剛性も影響するので、実はそれほどアテにならない。人間は、相対評価は得意でも、絶対評価は苦手だからだ。
コーナリングでボディ剛性を感じる領域となると走行性能の限界付近の領域になるから、サーキットでの試乗でもしない限りは現実には不可能。
ただし、コーナリング中にギャップがあったりすれば、ブッシュのチューニングの確かさなどと同時にボディ剛性の高さを感じ取れるかもしれない。
しかし、それ以前に前述のようにサスペンションの動き始めからボディ剛性は影響を与えているのだ。
サスペンションの動きに影響を与えるとなれば、クルマの動きにはそれ以上に影響を与える。
試乗記でも「ハンドリングが……」などと言われるが、曲がる性能にもボディ剛性は大きく影響している。
最終的にはホイールアライメントとタイヤの空気圧で調整されるハンドリングだが、やはりボディ剛性の影響は大きいのだ。
ダンパーやスプリング、ブッシュやスタビライザーといった足回りの特性を構成する部品の内容も大事だが、それを活かすも殺すも、その部品の支持剛性やボディ全体の剛性次第。
サスペンションがしっかり踏ん張っても、ボディがねじれたり、足回りの位置関係を歪ませてしまっては意味がないからだ。
コメント
コメントの使い方