■今後、大幅な軽量化の行方は炭素繊維強化プラスチック(CFRP)にかかっている!
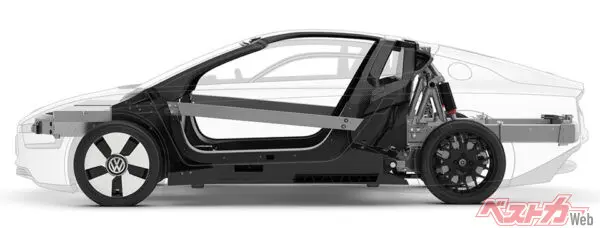
今後、ボディ材料としてもっとも期待できるのは、炭素繊維強化プラスチック(CFRP)だ。炭素繊維と合成樹脂との複合材で、CFRPに使用される炭素繊維はスチールの1/5、アルミの1/3の重量で強度、剛性に優れている。
今後、ハイブリッドカーやEVに欠かせない技術であり、さらなる軽量化を目指すためにはCFRPの量産向け技術が不可欠と考えられている。
しかし鋼材価格は1kgあたり百~数百円であるのに対し、CFRPは1万円以上と桁違いに高く、たとえ重量が減っても、そのコストは鋼材使用と比べ、10倍近く高価になる。
量産向け技術としては、従来のオートクレープ(圧釜)で加熱し、多くの時間、工数のかかる従来の工法から、現在では金型または樹脂型の内部にカットした炭素繊維のシートを重ね合わせる、または炭素繊維を編み上げた状態でセットした後、加圧した樹脂を注入、カーボンシートに含浸させた後に加熱や紫外線照射などにより硬化成形するRTM工法が、メーカーごとに開発されている。
このRTMでは従来のような大規模設備・少量生産が前提のオートクレーブを必要とせず加圧バッグやシール材などの廃棄物も発生しない。つまりオートメーション化が実現でき、これまでより安価にできるようになったのだ。現在メーカーごとに開発されているが、いずれにしても1部品あたり10分以内の成形時間を目指している。
今後の課題はクルマのモノコックフレームやサブフレームなどにCFRPが採用されるようになると、衝突安全性能をどう確保するかが大きな問題となる。CFRPは破壊されると鋭角の破片となって飛散するため、飛散の防止、衝突におけるエネルギー吸収性能を高める必要があるのだ。
そのためには衝撃吸収用の前後フレームはアルミ材とし、CFRP製モノコックキャビンと組み合わせる、またはカーボン繊維とほかの繊維を組み合わせて、衝撃吸収性能の優れたCFRPフレームを開発するなど、さまざまなことが考えられる。
おそらく2020年くらいまでにはCFRP部品が量産車種レベルまで採用される時代になるだろう。
■やり残したところがないほどあらゆる場所が軽量化
ボディ骨格以外の軽量化も近年、コンピュータシミュレーション技術(CAE)が5年ほど前から急速に発達してきたため、その加工技術も大幅に進化。
これまで、エンジンやボディ、シャーシなど車体構成部品のほとんどが、軽量化されてきたが、このCAEを使って、どの部材を適したところに配置できる過設計の段階から高度なシミュレーションが可能になったため、シャーシやボディ以外の軽量化箇所が大幅に増えてきたのだ。
特に内装材の軽量化が進んでいる。インパネやダッシュパネル、ドアトリムなど素材を薄くしながらもしっかりと強度を確保している。例えば、ミライースはインパネの樹脂製品やシートフレームの薄肉化で20kg軽量化。
なんと、スペーシアやプレマシーのシート骨格にまで超高張力鋼板が使われているのだから恐れ入る。スペーシアは前後シートで12kg、プレマシーはサードシート下のクロスメンバー下で約50%の軽量化。
また1台あたりの総重量が重いもので20kgにもなるワイヤーハーネスについても、軽量化のため、すでに銅からアルミ製に変わりつつある。実際の銅製に比べて、重量は平均で約2割安くなるという。
今後、約5割とされる高張力鋼板や高張力鋼板の採用比率が増えていくだけでなく、樹脂やアルミ、カーボンなどの材料置換のほか、徹底的に部材の薄肉化がますます進んでいくだろう。
* * *
コメント
コメントの使い方